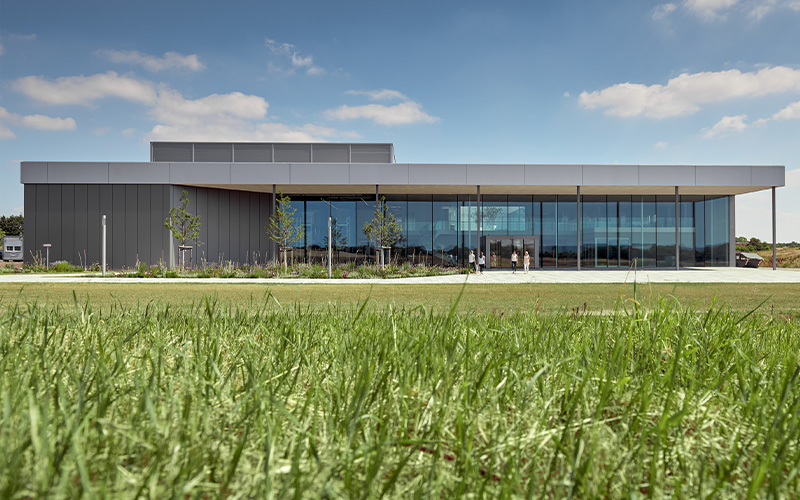
Simulation bei B. Braun: Fabrikplanungs-„Docs“ führen Fäden zusammen
B. Braun ist eines der weltweit führenden Unternehmen der Medizintechnologie. Das 1839 in Melsungen gegründete Unternehmen entwickelt intelligente Lösungen und setzt wegweisende Standards für den Fortschritt in der stationären und ambulanten Gesundheitsversorgung. Mit über 5.000 Produkten und wachsendem Fokus auf digitale Technologien unterstützt B. Braun Kliniken, Praxen, Apotheken, Pflegeeinrichtungen sowie Patienten. Auch in der Dialyseproduktion an den drei Dresdner Standorten Radeberg, Berggießhübel und Wilsdruff setzt B. Braun neue Technologien ein. Das 2018 in Betrieb genommene Werk in Wilsdruff bündelt alle für die Herstellung eines Dialysators notwendigen Prozessschritte unter einem Dach und ist zusätzlich in einem Produktionsverbund vernetzt. Jährlich werden hier mehrere Millionen Dialysatoren in unterschiedlichen Varianten produziert. „Wir sind jetzt bei 56 Varianten, was die Produktionsplanung deutlich komplexer macht“, sagt Ralf Aurich, Leiter Fabriksysteme bei B. Braun Avitum Saxonia. „Das hängt damit zusammen, dass Wilsdruff ein zweites Grundprodukt aufgenommen hat; hinzu kommen verschiedene Filtergrößen, regulatorische Anforderungen und Sterilisationsverfahren.“
Verschiedene Szenarien dynamisch prüfen
Eine Wirtschaftlichkeitsbetrachtung sollte anhand verschiedener Szenarien prüfen, unter welchen Bedingungen sich der Fabrik-Output verdoppeln lässt. „Wo sind Engpässe, wo müssen wir nachsteuern, zusätzliche Anlagen beschaffen und wie steuern wir die Produktion mit dem Ziel, den maximal möglichen Output zu erhalten?“, wollte Aurich wissen. Wegen der vielen Einflussfaktoren war eine herkömmliche Tabellenkalkulation keine Lösung. Eine dynamische Simulation mit Produktwechseln und nachträglicher Anpassbarkeit ließ sich intern aber nicht stemmen.
Um dafür alle Fäden zusammenzuführen, wandte sich Aurich an die Fabrikplanungs-„Docs“ bei LOGSOL, mit denen er bei einem Einstiegsprojekt bereits sehr gut zusammengearbeitet hatte. Wichtig war dem Leiter Fabriksysteme, „sich auch mal schnell treffen zu können“ – für die „Docs“ aus Dresden und Chemnitz gut machbar.
Für die Variantenvielfalt wollte B. Braun aus dem Simulationsprojekt Regeln für die Produktionssteuerung ableiten. Nach einem gemeinsamen Workshop konnte LOGSOL die Komplexität richtig einschätzen. In der Analysephase besichtigte Markus Störzel, Professional Logistics and Factory Planner bei LOGSOL, die Fabrik in Wilsdruff. Er fand es „sehr eindrucksvoll“, als er im Schutzanzug in die automatisierte Produktion im Reinraum durfte. „Für uns war die Datenbeschaffung als Grundlage der Simulation elementar“, sagt er. Die Fabrikkennzahlen wurden in einem Grob-zu-Fein-Vorgehen immer weiter aufgeclustert, bis sich verschiedene Produktvarianten mit unterschiedlichen Abrufmengen betrachten ließen, um die Gesamtleistung für das Werk in Wilsdruff ermitteln zu können.
Mehr als 1.200 Zeilen Programmcode
Dabei prüften die Fabrikplanungs-„Docs“ Materialfluss und Maschinenzahl auf Herz und Nieren, berücksichtigten unter anderem Zulieferprozesse für kleine Filtergrößen aus dem Werk Berggießhübel. Sie wollten bis ins kleinste Detail wissen, welche Parameter die Produktivität beeinflussen. Beispiel „Vorschub“: Aus der Geschwindigkeit, mit der die Spinnanlage die Faser produziert, resultieren Taktzeiten für Folgeanlagen, in denen die Fasern zu Bündeln aufgewickelt werden. Produktmixe, Puffer, einen höheren Spinnanlagenvorschub sowie andere Szenarien zu untersuchen, bedeutete enormen Aufwand: „Unsere Köpfe haben geraucht, weil wir alle Kombinationen durchspielen mussten“, sagt Störzel. Für das Simulationsmodell erstellte der Experte mit zwei Kollegen mehr als 1.200 Zeilen Programmcode.
LOGSOL übergab die Simulation als „Pack-and-Go“: „Wir haben die Datenbasis geliefert, damit B. Braun seine Business-Cases rechnen kann“, sagt Störzel. Auf Grundlage der detaillierten, praxisrelevanten Ergebnisse prüft das Medizintechnologie-Unternehmen verschiedene Szenarien bezüglich Rentabilität und Investitionen. Die Erkenntnisse sollen in ein APS-Tool (Advanced Planning and Scheduling) zur Produktionsplanung fließen, „um die Fabrik letztendlich so effizient wie möglich zu betreiben“, so Aurich. Auch in Zukunft wird B. Braun z.B. bei der Planung der Intralogistik auf das Know-how von LOGSOL zurückgreifen.