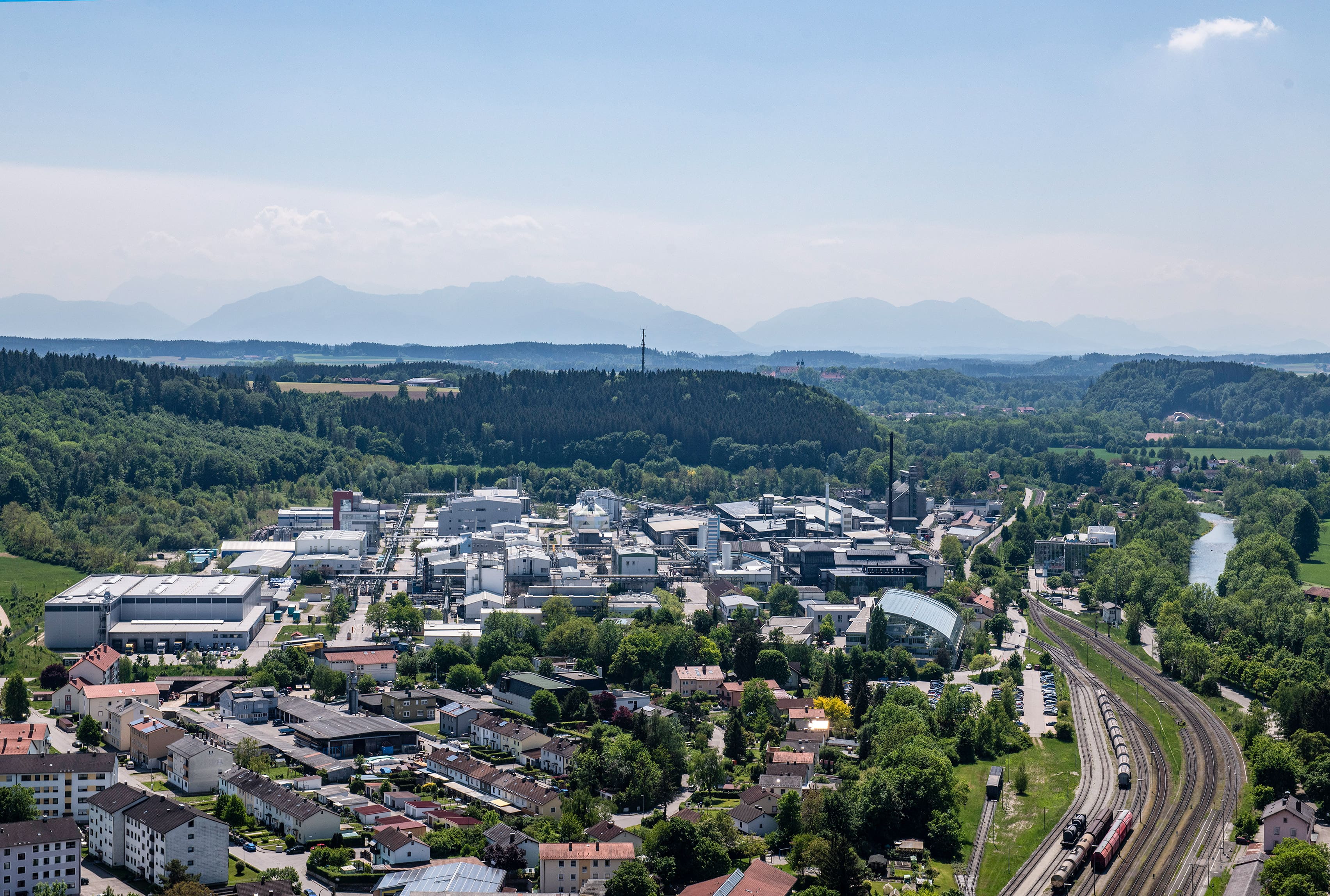
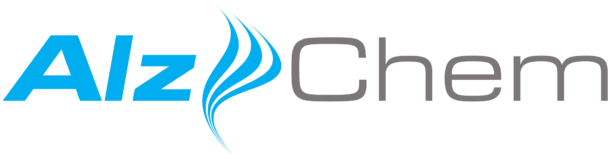
Introduction RampMan®
AlzChem Group AG is a globally active specialty chemicals company based in Trostberg, Upper Bavaria, in the district of Traunstein, and is one of the market leaders in most of its fields of activity.
The project
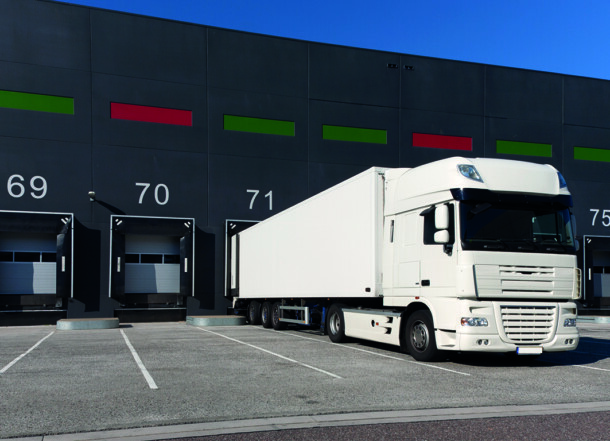
Due to unstructured pick-ups by the carriers at the plant in Trostberg and the associated workload peaks, a time slot management system was to be introduced. The aim was to use appropriate software to level out these peaks throughout the day and to make the pick-ups at the plant more predictable for the freight forwarders.
Integration of further ramps at the Trostberg Chemical Park
The special feature here was that, in addition to AlzChem, other companies in the Trostberg chemical park also use some of the ramps and therefore had to be integrated into the processes. All infrastructure services are provided by AlzChem, including storage and loading. AlzChem’s process involved transferring sales order numbers from SAP, which in turn could contain different items and delivery numbers. These were assigned to individual forwarders and storage locations (ramps).
The goals
One of the aims of introducing the software was to ensure that, after selecting the relevant customer orders, the forwarder can only book the ramp that is intended for loading the delivery numbers. After a market review and subsequent operational test phase, the chemical company decided to introduce RampMan®. RampMan® was able to completely cover the booking process of the other companies in the chemical park with the standard functions already implemented.
The implementation
Introduction phase 1
After a specification phase to define the interface and the downstream booking logic in November 2020, the programming implementation for the first phase began in January 2021. Due to the complexity of the project, it was initially divided into three phases. The first phase included a semi-automated interface (manual upload) between RampMan® and SAP to transfer the booking data. This included the customer orders and the assigned delivery numbers, including storage locations and carriers. Initially, new structures had to be created in the software in order to validate and save the transferred data for consistency on receipt. The next step was to adapt the RampMan® interface. Before the actual booking is made, the customer order number must be entered by the forwarders in order to display the approved ramps. Based on the selected ramp, ramp users will in future only be able to book the delivery number that belongs to the selected sales order, ramp and carrier. When the booking is saved, this validation is also carried out again to ensure the consistency of the data. This prevents future incorrect bookings, as ramp users can now only select their time slot for loading where the corresponding goods (represented by the delivery number) have been picked.
Introduction phase 2
After a four-week test phase, the implementations of the first phase have been operational since April 2021. Programming for the second phase began in parallel. This included the automation of the unidirectional interface for continuous data transfer from SAP. Manual uploading of order data has no longer been necessary since then, but is still possible. The implemented interface has been in use since May 2021.
Introduction phase 3
In the last phase, information on completed customer orders or delivery numbers was transferred from SAP to RampMan® in addition to the pure order data. As soon as a sales order is listed as completed in SAP, the set time is transferred to the time slot management system. This information is stored in RampMan as a time stamp for the booked time slots. This also allows the time recording for the truck’s exit to be carried out automatically. As a result, RampMan® immediately shows whether a time slot booking for this delivery number has already been completed or whether the truck is still on the factory premises or may be delayed.
The results
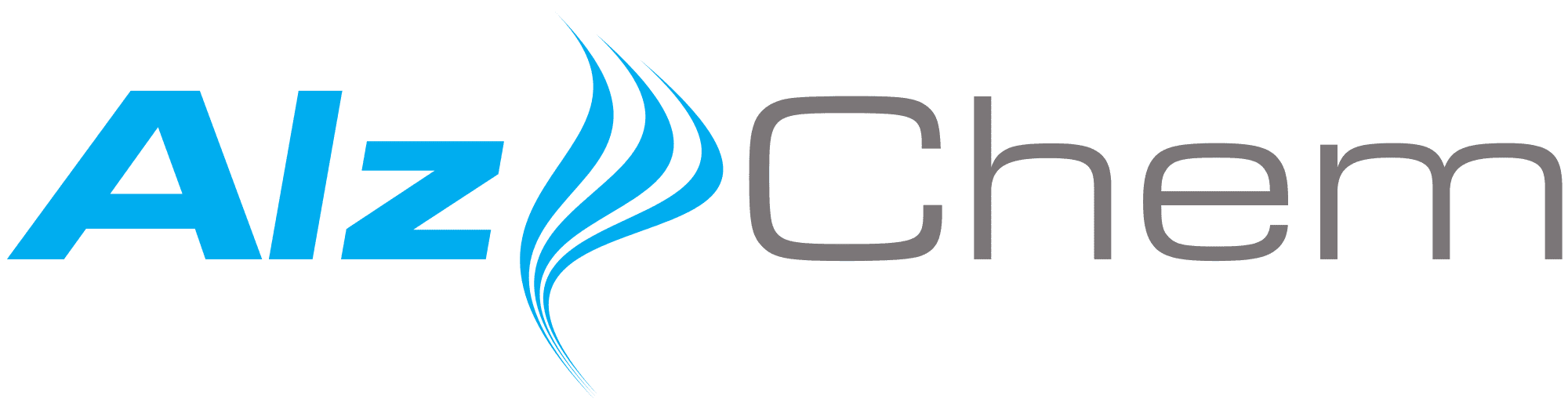
Dynamic times like these require both adaptability with a view to future trends and continuity with regard to tried and tested processes. The need to adapt logistics processes due to increasing sales capacities and the associated higher traffic volumes gave us the opportunity last year to launch a digital optimization project in collaboration with LOGSOL. […]
Alexander Russinger,
Supply Chain Management Project Manager Logistics, AlzChem Group AG
Further feedback from Alexander Russinger, AlzChem Group AG
“[…] The aim of the project was defined by the following framework conditions:
- A) To coordinate the volume of traffic at the Trostberg site (inside and outside the chemical park),
- B) to continuously maintain the loading capacities at a value-adding level and
- C) to increase transparency in the shipping process.
All these goals were achieved by introducing the RampMan® time slot management system. In simple terms, the system can be compared to a calendar in which a specific time must be reserved for loading each shipping order.
After almost 6 months of operational use, we at AlzChem can draw a positive conclusion and would like to thank LOGSOL once again for the successful and goal-oriented cooperation. Short, direct paths as well as a high level of expertise and empathy for our complex processes guaranteed the successful completion of this project.”
Other implementations already commissioned relate to the booking process and the user interface in RampMan®. For example, the customer-specific navigation in RampMan® is being optimized and a multiple assignment of customer orders to bookings is being implemented.
Download all the important information about RampMan® here.
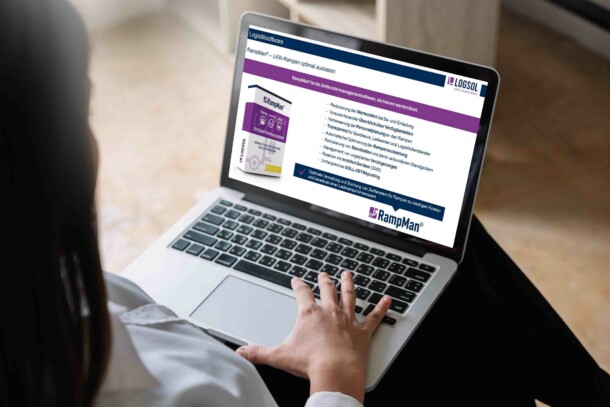
Relevant specialist areas
Would you like to find out more about our services?