Material flow simulation
With particularly dynamic or complex material flows, analytical methods reach their limits. With a material flow simulation, we offer you a comprehensible representation of your complex processes, which serves as the basis for important investment decisions. Digital models and simulation software are used to simulate and examine the behavior and movement of your materials, goods or merchandise in a system.
Customized material flow simulation: Your project, our expertise
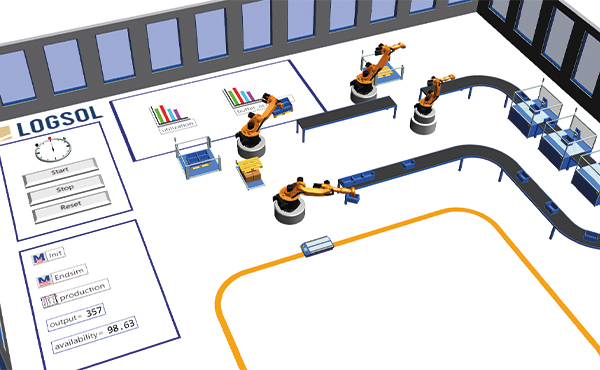
How LOGSOL optimizes your material flow
In material flow simulation, we visualize your logistics systems and fully map the production system. We use dynamic simulations to identify internal and external influences.
With our support, you receive a simulation model of your factory that helps you to save costs, shorten throughput times, increase productivity and flexibly adapt your production system to future requirements.
Procedure of a material flow simulation
1. Objectives and framework conditions
Together with you, we define the specific objectives of the material flow simulation, determine the area under consideration and identify the relevant boundary conditions and restrictions
2. Data collection and analysis
Relevant data sources are selected, the necessary input data is collected, processed and validated, and your current material flow is analyzed.
3. Modeling the system
The appropriate simulation software is selected, a basic model of the system is created, important process parameters and resources are defined, the material flow logic is modeled and the simulation model is checked for plausibility.
4. Carrying out the simulation
Various simulation scenarios are developed, the simulation is prepared and started, the results are collected and the simulation process is monitored and controlled.
5. Evaluation and analysis of the results
The data generated during the simulation is collected, compared with the targets, weak points and optimization potentials are identified and the effects of changes to individual parameters are analyzed
6. Optimization and improvement
Improvement strategies are developed, tested in the simulation model, the optimization results are analyzed and the measures to be implemented are selected.
Your advantages of a material flow simulation
The advantage of material flow simulation is that influences and changes can be analyzed without interfering with ongoing production. We run through various production scenarios for you, evaluate them and check their effectiveness and feasibility before a new implementation.
Your ongoing operations are not disrupted
Material flow simulations are cost-effective
Reduction of throughput times
Visualization of your processes in 2D and 3D
Flexibility in adapting to changes
Increased efficiency
Through material flow simulation, bottlenecks and inefficient processes can be identified and eliminated, resulting in improved material flow speed.
Competitive advantage
After optimizing your material flow, you can react faster and more cost-effectively to market requirements, which gives you an advantage over the competition.
Employee productivity
Optimized processes reduce your workload and employee stress, which increases productivity and satisfaction.
Process optimization
Simulations make it possible to uncover and eliminate weak points in your material flow, which leads to a more efficient use of resources. Unnecessary costs can thus be avoided.