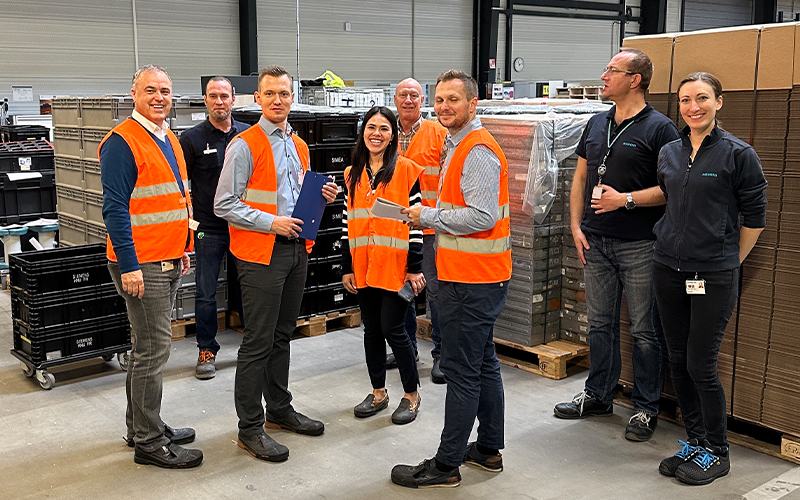
Sustainable Smart Container Management for Siemens AG Made by BinMan®
Siemens AG has set itself the goal of greater sustainability and efficiency in the supply chain. The aim is to intelligently design and control reusable container circuits and, at the same time, sustainably reduce internal processing costs.
Smart, smooth material flow plays an important role here. This is guaranteed only if the right load carrier is available at the right time in the right place during the production logistics process.
To achieve this in the future, BinMan® will be used as a web-based container management system, initially in five Siemens plants in Berlin (x2), Leipzig, Amberg, and Regensburg.
The aim is to increase the transparency of all container movements and optimize awareness of the condition and availability of all container types at the sites.
Each of the five plants is a closed system with different suppliers and material flows. The plants in Regensburg, Amberg, as well as the two in Berlin, already have an enterprise resource planning (ERP) system, which will be replaced by BinMan® at the end of this year.The first three locations, in Berlin (x2) and Leipzig, successfully launched BinMan® on October 10, 2022.
For the remaining two sites, go-live is scheduled for mid-December, and the BinMan® roll-out at further Siemens AG sites is scheduled for early 2023.
Container tracking in real time
At every Siemens AG site, a variety of containers in a wide range of sizes are used – including small-to-large crates, reusable plastic containers, wooden and plastic Euro pallets, mesh boxes, and train cars as “assets”. There are currently 83 container types and 269 connected suppliers at the five sites. Siemens AG is the owner of all load carriers used, including containers made available to suppliers for the provision of the required production materials. This ties up a lot of capital in the supply chain. In addition, it must be ensured that a sufficient number of intact containers is available to all suppliers “just in time” so that there are no delivery delays, deliveries in alternative packaging or – in extreme cases – production stoppages or time-consuming and costly container procurement.
With the introduction of BinMan® container management and its intelligent networking with existing systems, the container flow is transparent everywhere and at all times. The empty packaging dispatcher and the decision-makers can quickly and comprehensively view all information on the load carriers in real time using the BinMan® software, and respond proactively. A shared, transparent database is created with the supplier – including the four-eyes principle – without suppliers having to convert their own systems.
This enables active inventory management, such as precise inventory monitoring with stocktaking, as well as sustainable inventory optimization – with individual KPI reports for KPI-based decision-making.
Introduced efficiently and close to the standard
n the course of a preliminary project, two specification workshops were held in Berlin and Regensburg with representatives from the respective plants (Leipzig, Berlin, Regensburg, Amberg), to jointly agree on the details for the implementation project and to analyze corresponding gaps by determining the degree of coverage between software and process. Based on this gap analysis and the migration and rollout schedule, the introduction of BinMan® was specified in terms of content and cost. This was followed up by implementation and introduction of the software, including migration, training of key users and suppliers, as well as rollout and ramp-up. In general, BinMan® was launched very close to the standard. For the Amberg plant, which previously used a different ERP system, the software was adapted in order to map a specific process flow. After the closely standardized launch of BinMan®, further customized adaptations for Siemens AG are scheduled in upcoming phases.
Good cooperation and the prospect of more
What was special for us was that LOGSOL provided us with very comprehensive support from the first minute right up to go-live. All questions – and there were quite a few – were answered very competently by the LOGSOL project managers. We also felt entirely comfortable in terms of the software. From initial contact up to now, it’s been a very good partnership. We maintain very open communication and exchange ideas in a very constructive manner. The qualified two-day key user training courses in German and English, as well as the supplier training courses, have also been very well received and have contributed to the rapid acceptance of the new container management system.
And, of course, BinMan® pleasantly surprised us with its scope, both in terms of economic considerations and as an overall package. That’s why I’m convinced that, with the scope and performance of this product, we’ve found a future-oriented, sustainable software solution that can be rolled out at all Siemens plants”, says Thomas Exner, project manager for Supply Chain Management Logistics, Digitalization and Innovation, describing the special features of BinMan® and the LOGSOL team.
And LOGSOL project manager Dr. Sten Morawietz adds: “What was special for us was having Mr. Exner as a central contact for all plants. All the various strands come together here, and we’re able to collaborate very productively and on an equal footing. This enables us to work very effectively.
The system has already been set up and implemented at the plants, so that new plants can be integrated with little effort. Every subsequent plant can benefit from this valuable scaling effect.”
On October 10, 2022 the day the first wave of three plants went live, Sven Markert, Head & EVP of Supply Chain Business Company Smart Infrastructure at Siemens AG, posted the following on LinkedIn: “After weeks and months of hard work, we’re proud to announce that as of today, BinMan® is being deployed at three different Siemens sites. In the first step, we identified Siemens’ requirements and translated them into specifications for LOGSOL. BinMan® was also adapted to Siemens’ operational needs with specific software. This means that Siemens can rely on the capabilities of our BinMan® to increase container availability and inventory transparency, while sustainably reducing internal process costs. More sites are already waiting in line for the second wave in December 2022 and January 2023.”