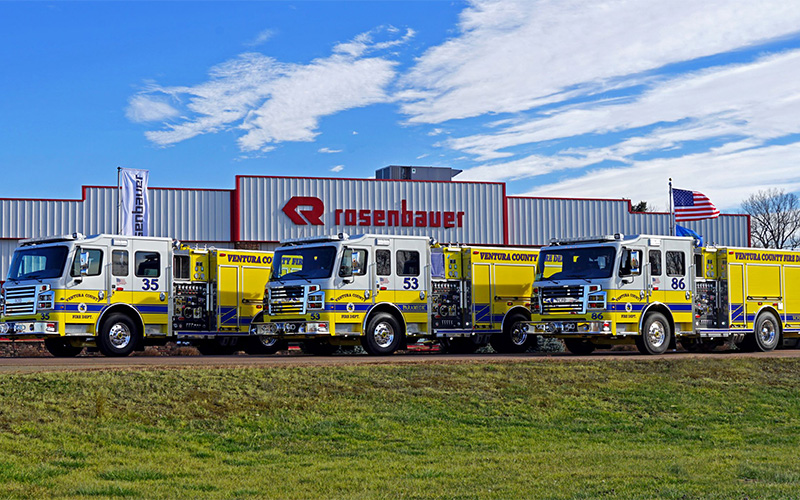
Logistics strategy for Rosenbauer: Successful planning of production sites in North America
With revenues of € 975.1 million, 4,100 employees and an international sales and service network in 120 countries (as of December 31, 2021), Rosenbauer is the largest firefighting equipment supplier in the world.
With its Strategy 2030, Rosenbauer is focusing on innovation and technology leadership, customer loyalty, operational excellence and sustainable and profitable growth. Based on this, strategic goals have been defined for all Rosenbauer America locations in Wyoming I + II, South Dakota and Nebraska in terms of growth, sales, revenues, vehicle integration and logistics optimization. These targets include doubling on-site vehicle production by 2030. LOGSOL was commissioned to work with Rosenbauer International managers to develop a sustainable logistics strategy for the Wyoming I (vehicle plant) and Wyoming II (chassis) production sites and to support the company in the area of strategic site planning.
Directly on site
The starting point was a joint on-site workshop in May 2022 at the Wyoming, Minnesota site. Here, a thorough inventory and analysis of all relevant current processes for inbound, in-house and outbound logistics and production was carried out. At the same time, a logistics quantity structure was created with the key figures relevant for planning. After an on-site kick-off, the data was transferred and recorded and the actual situation was recorded for all relevant influencing variables, with a focus on layout, processes, personnel and equipment. This formed the basis for a potential-oriented process analysis along the material flow and a list of relevant optimization topics. “Being on site together was important because the market, philosophy, working methods, technologies and vehicles are completely different in America than here in Europe. As a result, the production methods and steps are also different and this must be taken into account in our planning.
Historically, we have also worked with other IT systems. As an international company, we want to work with uniform standards worldwide. This means that the entire logistics systems, including materials management, have to be adapted and synchronized with our Group systems step by step,” says project manager Wolfgang Andreas Schettler from Rosenbauer International, describing the challenges of the project.
Professional approach in combination with excellent tools
“In just four days, we managed to create a really excellent inventory, even though a lot of the data simply wasn’t there and had to be collected from scratch. This created a valuable data basis on which we can now build as the project progresses. You can tell that the LOGSOL employees are full professionals, use excellent tools and have professional tools with which they carry out the data analyses. This works very smoothly, quickly and effectively,” continues Wolfgang Andreas Schettler from Rosenbauer International.
Sustainable rough concept planning
Based on the determined current situation, the second step from the end of May to the end of September 2022 involved planning the rough concept for a future-proof definition of production requirements for the expansion of the two production sites. In this context, functional areas and storage zones were dimensioned and the rough layout was created, taking into account given restrictions (e.g. building structure, land, material flow). As a result, the strategy was evaluated in terms of processes, personnel, layout, logistics equipment and logistics investment in a feasibility study. The necessary planning steps and the implementation schedule for 2022 to 2030 were then described in detail in a roadmap. The aim of the second step was to realign the processes to the needs-based dimensioning of the storage zones and to increase productivity and efficiency in the overall logistics context. In order to ultimately obtain planning security for the budget and the implementation period.
Iterative bringing together
The exciting and special thing about this project for all those responsible for the project was that the development of the production concepts by the Rosenbauer employees ran in parallel with the LOGSOL logistics planning that was coordinated with it. Both started at the same time and planned hand in hand. This meant that relevant logistical input could be integrated directly into the production planning. The project managers were able to exchange data directly via the Rosenbauer SharePoint server. “The joint planning progress of production and logistics went particularly well in this customer project. We did not work one after the other, as is so often the case, but in parallel. For example, when I planned a production plant including the production flow for a hall, I sent the design of what the assembly line or a production process would look like to the LOGSOL project manager Johannes Schönmetz.
Conversely, he provided me directly with the staging areas that he needed for the logistical planning of the stations, i.e. how much material and space should be provided for this station. The joint iterative bringing together and working together worked really well,” says project manager Wolfgang Andreas Schettler, describing the parallel work and progress.
Project challenges
“A good relationship of trust and working together as partners were extremely important for this project. We had to link three locations together: we planned from Austria, with LOGSOL from Germany, for the two production sites in North America. That involves a certain degree of complexity. And it has worked really well so far,” sums up project manager Wolfgang Andreas Schettler. “The particular challenges in this project were the geographical distance, the compact analysis on site within a week, the time difference and the conversion of all units between the two systems. In addition, a common technical vocabulary for logistics equipment and firefighting technology had to be established with all project participants. The partnership-based, open relationship as well as the cooperation and joint development in ping-pong mode were unique for us in this international project,” says Johannes Schönmetz, the LOGSOL logistics planner responsible, describing the special features of the project.
Outlook
Based on the result of the rough planning, the management of Rosenbauer International will decide whether it will be implemented in this form and at what time.
Due to the trusting and successful cooperation in the projects already realized, such as the logistics planning for the German location Mogendorf as well as for the main location Leonding, LOGSOL would be pleased to accompany this exciting project together with the Rosenbauer International project managers until its realization.