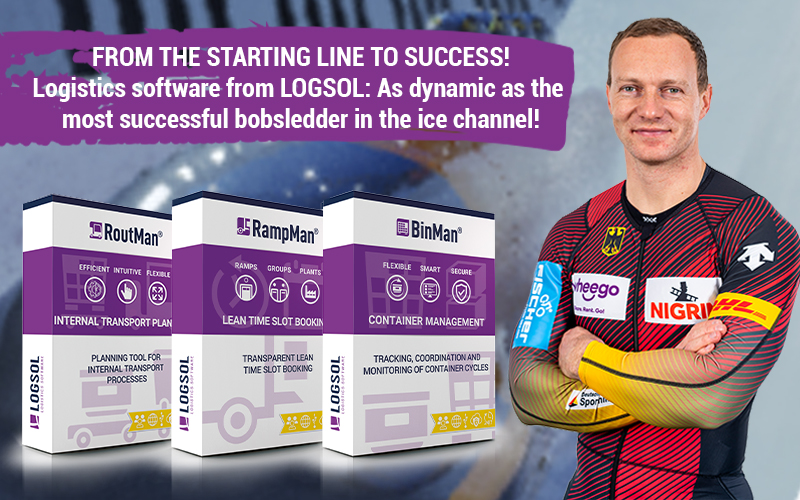
Clever logistics software solutions optimize your processes: Full overview of containers, ramps and in-house transports
Especially in economically challenging times, logistics chains need to run smoothly, but there are often friction losses with returnable containers and at the ramp. LOGSOL has developed scalable, web-based software solutions for these sticking points that provide industrial and retail companies with a 360-degree overview. This reduces logistics costs and increases efficiency.
BinMan® automates processes relating to container management: whether pallets, mesh boxes or Euro crates – it can be used to track, locate and manage all types of standardized load carriers. “Our logistics software not only demonstrably reduces process costs by up to 80 percent, but also minimizes container shrinkage and damage by the same amount,” says Dr. David Wustmann, Head of Logistics Software at LOGSOL.
Easy to use and key figures in real time: efficient software solutions for container management and ramp processes
The easy-to-use functions range from container planning using loading lists and supplier calendars to empties management using the ordering function and dispatch calculation. Real-time monitoring makes it transparent at all times where empty or full containers are located. The cockpit uses traffic light colors to clearly display important key figures, such as supplier stock levels. Red indicates a critical supply situation that can be precisely localized at the click of a mouse. Extensive analysis functions enable detailed booking processes or inventory evaluations. Graphical or tabular display options as well as automatic notifications and reports are particularly user-friendly.
“BinMan® also makes it much easier to exchange data with other systems and between different partners,” says Dr. David Wustmann, pointing out an important point. EDI interfaces are available for all common ERP systems, such as SAP/IDoc. The solution also supports various OEM and third-party portals, and booking reconciliations run automatically. Mobile data collection devices can also be integrated, for example tablets on the ramp.
The central communication platform RampMan® is used there, with which time slot management between ramp owners, suppliers and collectors can be organized smoothly. The interactive calendar view provides all users with a forward-looking overview of available slots. This makes productivity losses and demurrage charges due to long standing and waiting times at the ramp a thing of the past. “Even shippers with several locations in Germany and abroad can use RampMan® in their operations after just a short implementation phase. The web-based technology requires no on-site software installation and is multilingual,” says Dr. David Wustmann, citing key advantages.
Cloud solution takes real requirements into account
Booking data such as ramp number, start and end time or vehicle type are easy to enter, and time slots can be moved in the day view using drag & drop. The cloud solution is characterized by the fact that it takes real requirements into account: RampMan® displays delays, enables mobile actual time recording and sends text messages for journey control.
Thanks to extensive analysis options, companies can continuously improve their processes for optimal ramp utilization. This includes calculations of actual time deviations as well as tabular or graphical views for capacity utilization calculations – all automatically, of course. Export functions, including for PDF, facilitate evaluation. “RampMan® uncovers capacity peaks and bottlenecks, making it easier to plan not only ramp utilization but also connecting trips by freight forwarders,” emphasises Dr. David Wustmann.
Planning software supports procurement decisions
Planning effort and costs for internal transport processes can be significantly reduced with RoutMan®. The intuitive planning software is suitable for strategically planning forklift transports or automated guided vehicles (AGVs) and supports procurement decisions, for example. “Key figures relating to profitability or capacity utilization can be determined efficiently and different scenarios can be compared because RoutMan® uses established calculation methods in accordance with the Association of German Engineers standard,” explains Dr. David Wustmann. This significantly reduces the burden on operational workflows: input parameters are automatically generated for subsequent control, processes as well as hall layouts and route networks are dynamically visualized. Of course, all relevant route characteristics such as encounter traffic or turning options are taken into account. Users also appreciate the detailed view of critical time intervals.
Thanks to years of cross-industry project experience, LOGSOL knows the different requirements and therefore offers the software solution as a complete or service package as well as software-as-a-service for a specific period of time. “RoutMan® not only helps to avoid empty runs and therefore costs. Our logistics software also increases energy efficiency and prevents accidents involving forklift trucks or pallet trucks,” emphasizes Dr. David Wustmann.
LOGSOL programs individual solution modules into its standard software or completely new applications for special requirements. This ranges from table filters, graphical evaluations or automatic e-mail dispatch to interfaces and new web applications. “We follow the agile principle, programming in a lean and flexible way. The software follows the process, not the other way around,” says Dr. David Wustmann.
There is an even better overview on the LOGSOL website, where three videos present important functions of BinMan®, RampMan® and RoutMan® in a visual and easy-to-understand way.