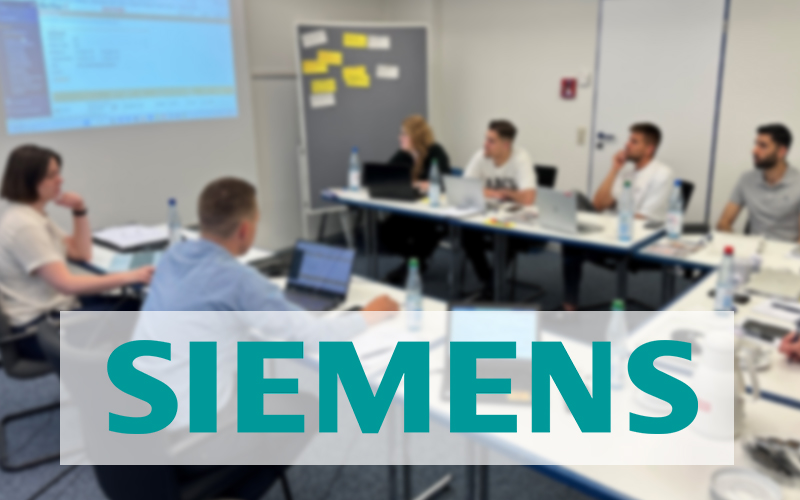
BinMan® at SIEMENS AG: Huge steps towards sustainability
At a time when environmental protection is becoming increasingly important, it is crucial for large companies to develop innovative solutions to minimize their ecofootprint while operating efficiently. Siemens AG relies on the pioneering technology of BinMan®, because transparent container management significantly improves sustainability.
The advantages of transparent container management are numerous. On the one hand, it enables more precise planning and optimization of ordering and collection processes. This leads to fewer emissions and resource consumption due to transport. For another, companies like Siemens AG can more easily identify which load carriers can be reused or recycled instead of wasted. This not only reduces costs, but also environmental impact. An additional important aspect is the ability to collect and analyze real-time data. This enables Siemens AG to identify trends in resource consumption. These findings serve as the basis for strategic decisions to further improve sustainability. Since LOGSOL began introducing sustainable smart container management with BinMan® at Siemens AG over a year ago, the extensive project has progressed with huge steps. “We are currently in the connect phase and have already connected twelve plants,” says Thomas Exner, Project Manager Supply Chain Management Logistic, Digitalization and Innovation, summarizing the interim status in September 2023. Since the first go-live wave in October 2022, the business units Digital Industries, Smart Infrastructure and Mobility as well as the company Innomotics have each been working as a closed system with LOGSOL’s web-based container management software at various German locations between Berlin, Leipzig and Nuremberg. The French Siemens AG plant in Hagenau is also already utilizing BinMan®.
Transparent container overview across plants
Thomas Exner is thrilled that BinMan® provides a 360-degree overview across all load carriers: “We know exactly which supplier has which containers, and we can track and optimize the routes.” The plan is to “connect further plants so that we can obtain the greatest possible transparency within Siemens AG,” he says. By the end of 2023, BinMan® will also be used in Erlangen, Rastatt and Sibiu (Romania). This will increase the number of connected plants to 15. The more available data for evaluation, the better – “because this is the only way to create maximum transparency in combination with the greatest possible benefit,” explains Dr. Sten Morawietz.
Evaluate key figures in the dashboard for sustainability
The LOGSOL team plans to build a management dashboard for Siemens AG, that specifies as well as quantifies selected Key Performance Indicators (KPIs) in container management. The planned diverse business analysis and evaluation options of BinMan® have enormous evaluation potential. Currently, LOGSOL is further developing an internal dashboard with the ability to forecast selected KPIs based on statistical forecasting models. “For example, if we provide suppliers every two days, it’s a great thing to learn via the dashboard in the future that once a week would be sufficient,” says Thomas Exner. So it makes sense to optimize sustainability within the company through active container management. “We want to support Siemens AG in sustainability evaluation. BinMan® provides the data gold for this,” says Dr. Sten Morawietz. How many delivery processes do I have? How much cardboard do I need to dispose of? “This all contributes to sustainability and CO2 reduction,” he emphasizes. The LOGSOL Project Manager stresses: “The more Siemens AG plants are involved in the future, the better the flashlight in my black box shines, and I know where I can save a lot with just a few measures.”