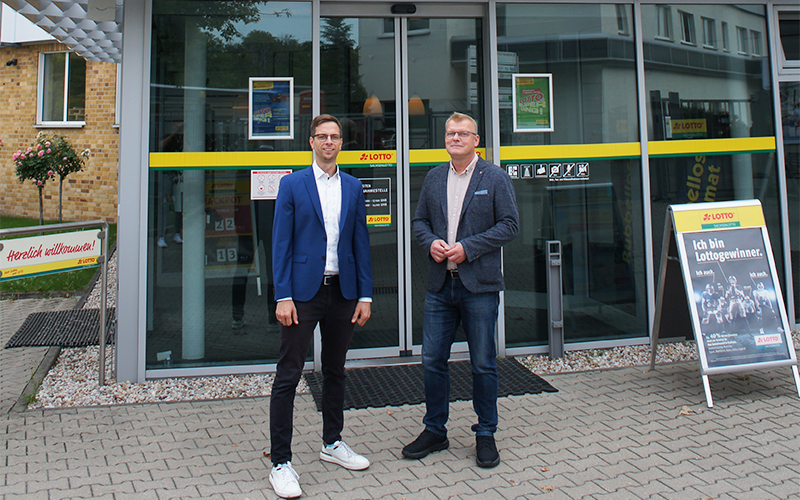
How much of a role does logistics play in bringing us our lottery tickets?
LOGSOL was commissioned by Sächsische Lotto-GmbH to review and design a future-oriented, overall logistics concept across all logistics processes.
This was a very exciting task for those in charge of the LOGSOL project. When it comes to lotto, most people just think of the lottery tickets.
Logistics plays a big role
Sächsische Lotto-GmbH has around 130 employees. Contract partners at the 1,250 outlets employ approximately 5,000 sales staff.
The supply of this large outlet chain with lottery tickets, scratch cards, marketing materials, and sales communication is currently managed in a two-stage logistics process:
The materials are delivered to the central warehouse at the company’s site in Leipzig. This is where outlet-specific ordering and courier dispatch to the two district offices in Dresden and Chemnitz take place. The Leipzig district office is located at the company’s site and is supplied directly. From the district offices, the respective outlets are supplied by courier.
For example, from the Chemnitz district office, 24,000 courier boxes are delivered annually to 467 outlets, in addition to materials sent separately, such as sidewalk displays, which are sent as bulky goods.
This two-stage logistics process was examined by LOGSOL’s consulting specialists with regard to economic efficiency, process reliability and optimization potential. The aim was to develop a recommendation for an optimized logistics process for Sächsische Lotto-GmbH and to present this as a basis for decision-making.
A professional perspective is sought
After the project kicked off in November 2021, an analysis was carried out by LOGSOL project managers. In the first phase, an inventory was taken and the actual processes on site were observed, monitored and queried in person. The direct oversight of employees on site, the professional overview of all workflows and processes, and the in-person survey all combine to provide the required up-to-date, realistic overview for the creation of a feasible, optimized concept. By interviewing the relevant operational employees, the data on executed workflows and time requirements could be collected directly and validated in parallel using an MTM.
An example of one very specific logistical challenge relates to the central warehouse, which has storage facilities located on different levels at the Leipzig site. For the logistics staff this means covering long distances and switching levels and work equipment (trolley, pallet truck, forklift) during transport. Based on the analysis data collected and a process analysis focusing on vulnerabilities, a process flow diagram and an optimization list were created.
These were fine-tuned and validated in a first milestone presentation in collaboration with Sachsenlotto.
Identifying new potentials and future scenarios
This documentation subsequently serves as a data and planning basis for evaluating and developing optimized future-oriented concepts for what has so far been a two-stage logistics process for Sachsenlotto. The focus was on the following questions: At which points can the current logistics concept be optimized? Which processes can be economized or streamlined? What future scenarios need to be considered? What can be implemented in the short term, medium term, and long term and in what way? Which economization potentials have been identified from a commercial point of view, but also from a process-oriented point of view, with regard to process robustness and security?
Six concept variants emerged, and these are being coordinated with Sachsenlotto in a first intermediate step with regard to internal feasibility and implementation barriers (such as IT and data protection factors).
Jointly prepared for the home stretch
Four of the concepts made the cut. For each of these, a utility analysis and a qualitative assessment were prepared by LOGSOL specialists to provide decision-making support. The analyses were presented and jointly approved in a workshop with ten Sachsenlotto experts from sales, marketing, and logistics, including those responsible for interim storage.
The recommendation for the design of a logistically optimized overall concept, including alternatives, was presented to the decision-making body in March 2022, right on schedule. This clearly outlines, from an independent expert point of view, the questions of what, when, how, and with what effort. “We had to start the project under tight pandemic restrictions, however, thanks to the professionalism and flexibility of LOGSOL’s project managers, there were no delays or project interruptions and we remained on schedule throughout”, concludes project manager Steffen Holz, Purchasing Manager at Sächsische Lotto-GmbH.
LOGSOL is eager to see which concept will be chosen, and is ready to assist Sächsische Lotto-GmbH with its realization, e.g. with competent support in tendering and selection of the best implementation partners. So that the annual 60,000 courier boxes are delivered even more efficiently to the 1,250 outlets and everyone can always fill in their lucky lotto ticket on time.