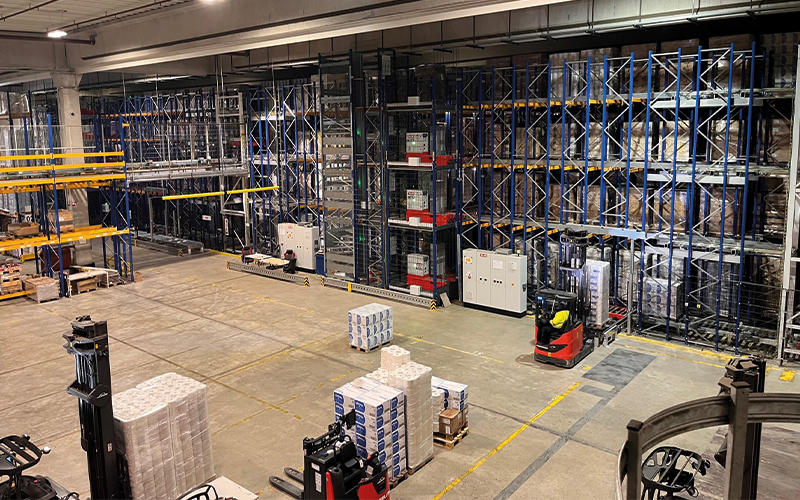
Demanding paperwork: Warehouse consolidation for Kimberly-Clark
When Christoph Mueller stood in front of empty toilet paper shelves in the supermarket during the first Covid lockdown, he had no idea that this would soon concern him professionally. In September 2020, the Senior Logistics and Factory Planner at LOGSOL took on a project in Koblenz in the hygiene paper industry at Kimberly-Clark (KC). They are known for brands such as Kleenex or Scott and with around 45,000 employees worldwide. Christoph Mueller was attracted by the challenging task. “The existing warehouse had to almost double its capacity during ongoing operations – from just under 27,000 to around 45,000 pallets.” In the immediate vicinity, KC’s paper mill incessantly produces toilet paper, wipes and towels. In the future, everything is to run completely automatically from production directly into a highly compact automatic rack.
One-stop conception and realization for Kimberly-Clark
By mid-2024, KC plans to consolidate three external warehouses in its Central European distribution center in Koblenz. Everything has to be accommodated in the existing building on approximately 27,500 square meters. KC needed a reliable partner for this large-scale, multi-year project. According to Kimberly-Clark, LOGSOL’s “expertise in the conceptual design and implementation of such strategic projects” was convincing.
LOGSOL successfully completed the preliminary project in just three months by the end of 2020. “Conception is our daily bread,” comments Christoph Mueller. With his team, he created logistics concepts, compared and evaluated them with regard to throughput, capacity, costs, feasibility. They looked at just about everything the market has to offer – from block storage to wide-aisle and narrow-aisle pallet racking to drive-in rack, push-back racking, shuttle storage and storage with stacker cranes. With the help of LOGSOL’s business case tool, five variants could be evaluated in monetary terms. The experts recommended a shuttle storage with electric vehicles for the automatic operation of rack storage. After this key decision template, the real challenge in project management as well as in detailed planning, procurement and run-up planning was yet to come.
“We don’t push together nice slides and then wish good luck, but rather accompany our customer throughout the entire project, all the way to commissioning,” clarifies Christoph Mueller. The four-step implementation at KC began in 2021. In the meantime, “we have successfully integrated the first external warehouse in Koblenz,” informs Kimberly-Clark. Anything but a routine job, because automation technology and an SAP-based Warehouse Management System were introduced at the same time. By April of next year, another external warehouse is to be integrated. Followed in the final step by the Koblenz buffer storage – “then we would be through by the middle of 2024,” Kimberly-Clark hopes. Because not everything always goes according to plan.
Inventory forecast and project schedule under control
“In the course of the project, new circumstances arise again and again, and LOGSOL reacts very well to them,” is the positive feedback of Kimberly-Clark. Example: As a result of the hygienic paper panic buying, retailers had ordered large quantities. The Koblenz warehouse was completely full, including the buffer storage. “Stocks were far too high and had to be brought down so that we could continue building the automatic rack,” comments Kimberly-Clark. In this critical situation, the project team had to find a solution quickly. With his colleague, Christoph Mueller created transparency and customized LOGSOL’s inventory planning tool for continuous projection of the inventory situation. “LOGSOL developed a visualization that takes into account our inventory forecast and, at the same time, the project schedule with available capacities,” says Kimberly-Clark.
Conclusion of the customer: “For us it was a huge advantage to have a partner who actively supports us on site in critical situations.” The company would also like to approach LOGSOL in the future to further optimize logistics processes at KC. Christoph Mueller looks forward to being wrapped up again by the hygiene paper industry in order to roll out exciting projects.