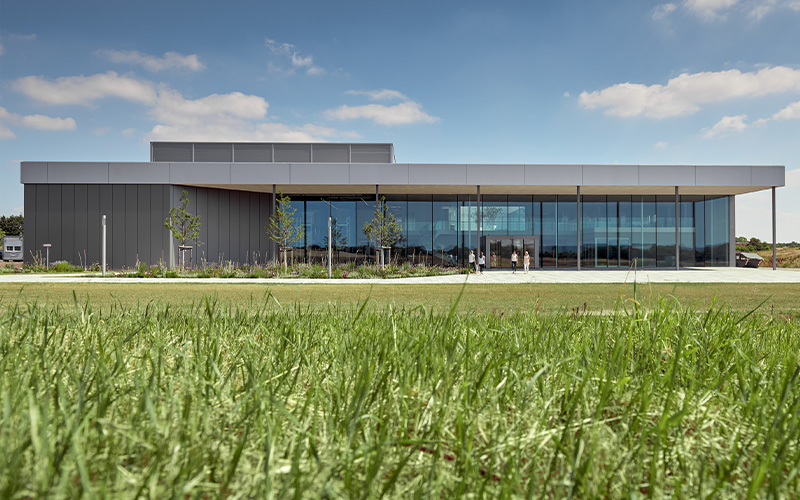
Simulation at B. Braun: Factory planning “docs” bring threads together
B. Braun is one of the world’s leading medical technology companies. Founded in Melsungen in 1839, the company develops intelligent solutions and sets pioneering standards for progress in inpatient and outpatient healthcare. With over 5,000 products and a growing focus on digital technologies, B. Braun supports clinics, medical practices, pharmacies, care facilities, and patients. B. Braun also uses new technologies in dialysis production at its three Dresden sites in Radeberg, Berggiesshuebel and Wilsdruff. The plant in Wilsdruff went into operation in 2018 and combines all the process steps required to manufacture a dialyzer under one roof and is also part of a production network. Several million dialyzers in different variants are produced here every year. “We now have 56 variants, which makes production planning much more complex,” says Ralf Aurich, Head of Factory Systems at B. Braun Avitum Saxonia. “This is due to the fact that Wilsdruff has added a second basic product, as well as different filter sizes, regulatory requirements and sterilization processes.”
Dynamic testing of different scenarios
An economic feasibility study had to examine the conditions under which factory output could be doubled using various scenarios. “Where are bottlenecks, where do we need to make adjustments, procure additional equipment, and how do we control production with the aim of achieving the maximum possible output?”, Aurich wanted to know. Due to the many influencing factors, a conventional spreadsheet calculation was no effective solution.
owever, a dynamic simulation with product changes and subsequent adaptability could not be managed internally. To bring all the threads together, Aurich turned to the factory planning “docs” at LOGSOL, with whom he had already worked very well on an initial project. It was important to the Head of Factory Systems “to be able to meet quickly” – something that the “docs” from Dresden and Chemnitz could easily do. For the range of variants, B. Braun wanted to derive rules for production control from the simulation project. After a joint workshop, LOGSOL was able to assess the complexity correctly.
During the analysis phase, Markus Störzel, Professional Logistics and Factory Planner at LOGSOL, visited the factory in Wilsdruff. He found it “very impressive” when he was allowed to enter the automated production in the clean room in a protective suit. “For us, data acquisition was fundamental as the basis for the simulation,” he says. The factory key figures were clustered further and further in a rough-to-fine approach until different product variants with different release quantities could be examined, in order to determine the overall performance for the plant in Wilsdruff.
More than 1,200 lines of program code
The factory planning “docs” put the material flow and number of machines through their paces, taking into account, among other things, supply processes for small filter sizes from the Berggiesshuebel plant. They wanted to know down to the smallest detail which parameters influence productivity. Take “feed rate”, for example: The speed at which the spinning system produces the fibers results in cycle times for downstream systems, in which the fibers are wound into bundles. Investigating product mixes, buffers, a higher spinning system feed rate and other scenarios meant an enormous amount of work: “Our heads were spinning because we had to run through all the combinations,” says Störzel. The expert and two colleagues created more than 1,200 lines of program code for the simulation model.
LOGSOL handed over the simulation as a “pack-and-go”: “We provided the database so that B. Braun could calculate its business cases,” says Störzel. Based on the detailed, practical results, the medical technology company is examining various scenarios in terms of profitability and investment. The findings will flow into an APS tool (Advanced Planning and Scheduling) for production planning, “in order to ultimately operate the factory as efficiently as possible,” says Aurich. B. Braun will continue to rely on LOGSOL’s expertise in the future, for example when it comes to intralogistics planning.