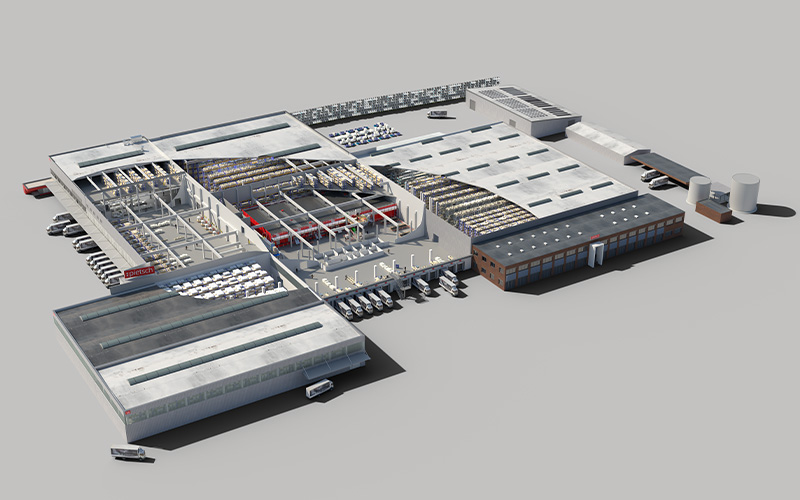
AutoStore: Clever warehouse automation at Pietsch
In Germany, sinks, showers and toilets are part of every bathroom, while towel radiators and urinals are less common. As a leading wholesaler for sanitary, heating, environmental, air conditioning and ventilation products, the Pietsch Group from Muensterland has 44,000 items permanently available in four central warehouses in Germany. The logistics division, Logistik4YOU, ensures that customers receive the right quantity of goods on time. As Head of Logistics, Frank Leupers is proud of the optimized processes with 99.7 percent error-free picking. However, in 2019, the capacity of the 35,000-square-metre warehouse at the company’s headquarters in Ahaus reached its limit – the situation was reminiscent of the morning rush hour when everyone has to go to the bathroom at the same time: Goods were being taken to areas where they didn’t belong, transports were being made twice, and ABC distribution could no longer be carried out. In addition, the new mail order company COLONS enjoyed growing sales.
Trust, pragmatic approach and detailed knowledge
LOGSOL was the partner of choice for strategy consulting, logistics planning and tendering support for site development, because a “basis of trust” has existed for almost a decade thanks to previous projects in Muelheim/Ruhr and Ostrau in Saxony. “The pragmatic approach at equal level” makes the logistics manager’s work easier: “Our business is understood with detailed knowledge of our processes and product ranges.”
The project in Ahaus started in 2020 with a strategy workshop that presented various growth options with variants on transport and warehouse technologies. Bastian Scheu, Principal Logistics and Factory Planning at LOGSOL, found it exciting “to have a holistic view of the corporate strategy and analysis of the locations within the company network”. With LOGSOL’s Business Case Tool, he was able to keep an eye on all costs during the rough concept phase. Pietsch opted for an automated small parts warehouse from AutoStore due to the high throughput, an economical amortization period and the lack of space and skilled workers. Leupers was impressed by the very compact warehouse design, which requires “significantly less space”.
AutoStore: Pulsating warehouse heart with 61,500 boxes and 23 robots
The technologies were specified until 2022 so that they could then be put out to tender on the market. As a certified AutoStore consultant, LOGSOL was able to impress in the detailed planning phase: “AutoStore is the pulsating heart at the center of the Ahaus site and will be expanded with various conveyor technologies and automation options, such as an automated packaging line for cartons,” explains Scheu. Leupers likes to explain warehouse automation as an oversized Lego kit: “There are 23 robots on top and 61,500 boxes underneath, as if assembled from Lego bricks.” Sounds simple, but requires a high level of consulting expertise. The 5.40 meter high cube has neither aisles nor spaces in between. Everything works automatically – “the 23 new colleagues” move around the AutoStore without a break, storing and retrieving goods, saving warehouse employees many kilometers of walking and increasing productivity. “In future, 65 percent of our daily output will come from this system,” Leupers says.
AutoStore had to be implemented during ongoing operations, LOGSOL developed a relocation plan for Pietsch that could be implemented step by step without disrupting day-to-day business. In addition to the modern small parts technology, the site also received a new warehouse for around 6,000 pallets. “We have invested around 20 million euros in warehouse and facility technology. We have added 10,000 square meters of storage space, and we have saved a significant amount of space by implementing our AutoStore automatic small parts system,” summarizes Leupers with great satisfaction. This point is particularly important to him: “During the entire relocation phase, we didn’t stop operations for a single day.”
As a result, LOGSOL was awarded the follow-up contract to also plan the new Pietsch warehouse location in Bremen for fittings, pipes and other items, as well as an AutoStore for small parts.